工場建設の最終段階!本稼働前に重要な試運転の内容とサービス | 工場建設パーフェクトガイド
工場建設の流れ
工場建設の最終段階!本稼働前に重要な試運転の内容とサービス
公開日:2024.03.27 更新日:2024.03.27
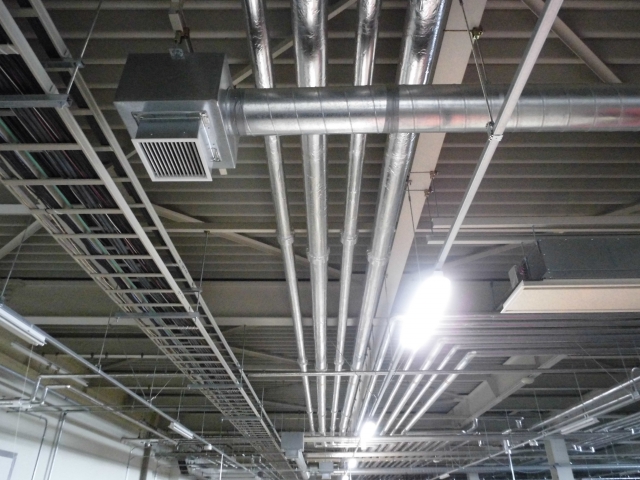
工場建設の試運転は、設備や機器の正常な動作や性能を確認する最終段階であり、安定した稼働と効率的な生産を保証します。設備不良は生産性や品質に影響を与え、損失を招くため、初期不良を確認してトラブルを防ぎます。製紙プラントの場合、水回し運転から始め、機械や制御システムの動作を確認し、最終的に生産ラインの安定性や省エネルギーをチェックします。
試運転は時間と手間がかかるため、自動化サービスが提供され、試運転時間を短縮し、髙丸工業のサービスでは、新しい生産ラインの試運転を旧ラインの停止なしに行うことで、時間とコストを節約し、リスクを回避します。
目次
本稼働前の最終チェック!試運転の重要性
工場の建設が終わり、官公庁による検査が無事に終了した後には、本稼働前の最後の段階として試運転が待っています。
試運転の目的と重要性
試運転は、工場建設における重要なプロセスであり、機器や設備が正常に稼働し、仕様通りの性能を発揮するかどうかを確認するために行います。試運転では、以下のような作業が行われます。
試運転では、細かい調整や確認を行うことで、工場の安定した稼働や効率的な生産活動を実現するための基盤を整えます。十分な準備と計画を立てて、試運転を徹底的に行うことが重要です。
試運転で確認する主な内容
試運転でまず確認するのは、機器の起動と動作確認です。正常に起動するかどうか、あるいは動作が安定しているかどうかを確認し、必要に応じて調整や修正を行います。また、機器や設備が仕様通りの性能を発揮しているかどうかを評価することも大切です。
試運転中には、この他に安全性の確認も行います。問題点や不具合がある場合には、適切な対策や修正を行い、本稼働時にトラブルが発生するリスクを最小限に抑えます。
工場の設備不良は損失に繋がる
工場の設備が正常に機能しない場合、さまざまなトラブルが発生する可能性があります。トラブルが重なると生産性が上がらず、ひいては損失に繋がることも考えられます。
設備不良によるトラブル
工場で起こるトラブルの中でも最も多いのが、設備不良によるトラブルです。設備の不良により生産ラインが停止すると、生産量が減少し、売り上げの減少や納期遅延が生じます。
また、設備の不良により品質が低下し、不良品が生産される可能性があります。不良品の廃棄や再加工によるコスト、顧客からのクレームによる信頼の低下などによって、損失が発生します。
設備の試運転で初期不良の有無を確認
工場の損失を防ぐためには、試運転で初期不良がないかどうかを確認することが大切です。本稼働前に問題点を解決しておくことによって、不良品の発生や生産中の停止などを防ぐことができます。
それだけではなく、試運転を通じて、作業者に対する適切な訓練や操作方法の習得を促すことができます。作業者が正しく設備を操作し、トラブルに対処できるようにすることで、生産効率を向上させることができます。
工場建設の試運転の様子を紹介
プラント建設の試運転は、機器や設備の取り付けと配線、プロセスの設定などといった準備作業を済ませた上で行われます。
プラント建設を例に試運転の内容を解説
製紙プラントの場合には、最初に原料を投入せず、水だけで運転をする「水回し運転」を行います。水回し運転の段階で機械だけではなく、電気などに不具合箇所がある際には手直し工事を行います。次に制御システムやセンサーの動作確認、各種バルブ・弁の操作テストなどのシステムテストが行われます。調整が必要な箇所があれば、ここで設備や制御パラメーターの調整を行います。
その後、実際に原料を投入してのプロセス試験と安全確認に入ります。製品が支障なく製造され、品質や生産能力が確認された後は、省エネルギーや環境リスクの面がきちんとクリアされているかをチェックします。
時間のかかる試運転をサポートするサービス
試運転は時間がかかり、工程も煩雑なため、作業員が手作業で実施すると、操作ミスによってエラーが発生する可能性があります。ですから、試運転をソフトウェアによって自動化するサービスを活用したり、専門家による技術サポートを受けたりすることによって、試運転にかかる時間を短縮し、作業員への負担を軽減することができます。
工場設備の試運転を自動化
工場設備の試運転を自動化するソフトウェアの中でも代表的なのが、シュナイダーエレクトリックの「EcoStruxure Field Device Expert」です。このソフトウェアは、同社の分散型産業用機器制御システム「EcoStruxure Foxboro DCS(Distributed Control System)」の追加用ソフトウェアとして開発されたもので、工場ならびに各種プラントにある設備の試運転を自動化する機能「インテリジェント コミッショニング ウィザード(Intelligent Commissioning Wizard)」が含まれています。
インテリジェント コミッショニング ウィザードを利用することによって、週7日、1日24時間、年中無休でデバイスの試運転ができるだけではなく、追加コストも不要です。2018年9月13日に発表されたこのソフトウェアは、手作業と比較した場合、試運転にかかる時間を75%以上短縮できる点がメリットです。
現在の稼働を止めずに新規の生産ラインを確認
髙丸工業の試運転調整業務も、工場の現在の稼働をストップせずに試運転ができるという画期的なサービスです。髙丸工業が有する大型工場(25m✕200m)にユーザーの生産ラインと同じレイアウトをあらかじめ再現しておき、完全な試運転を行います。ですから、旧ラインでの生産を止めずに、新規の生産ラインに不具合がないかどうかを確認できます。
このサービスを利用することによって、旧ラインから新ラインへの以降によってロスする時間を最低限に抑えることが可能になります。時間とコストの大幅な削減ができるだけではなく、リスク回避にも貢献しているのがラインビルドサービスの特徴です。
工場建設の最終段階である試運転は、機器や設備の正常な動作と性能を確認する重要なプロセスです。試運転では、機器の起動や動作安定性、仕様通りの性能を確認し、必要に応じて調整を行います。また、安全性も重視され、トラブル発生時の対策も確認されます。これにより、安定した稼働と効率的な生産が確保されます。
工場の設備不良は生産性の低下や品質の低下など様々なトラブルを引き起こし、損失につながる可能性があります。特に、生産ラインの停止や不良品の生産によって売り上げ減やコスト増が生じます。試運転では初期不良を確認し、問題解決や作業者の訓練を行うことで、トラブルの防止や生産効率の向上が図られます。
工場建設の試運転は機器の設置や配線、プロセスの設定などを終えた後に行われます。製紙プラントの例では、まず水回し運転を行い、機械や電気に問題がないかを確認します。その後、制御システムやバルブの動作テスト、調整作業を行います。原料を投入してプロセス試験を行い、製品の品質や生産能力を確認した後に、省エネや環境リスクのチェックを行います。
試運転は時間と手間がかかるため、手作業ではエラーが起こる可能性があります。そこで、試運転を自動化するサービスが提供されています。例えば、シュナイダーエレクトリックの「EcoStruxure Field Device Expert」は工場設備の試運転を自動化し、試運転にかかる時間を75%以上短縮します。また、髙丸工業のサービスでは、現行ラインを停止せずに新しい生産ラインの試運転を行います。これにより、時間とコストを節約しつつ、リスクを回避できます。
工場建設パーフェクトガイドでは、工場建設を成功に導くための方法や工場建設に関する情報を掲載しています。ぜひ他の記事もご覧ください。
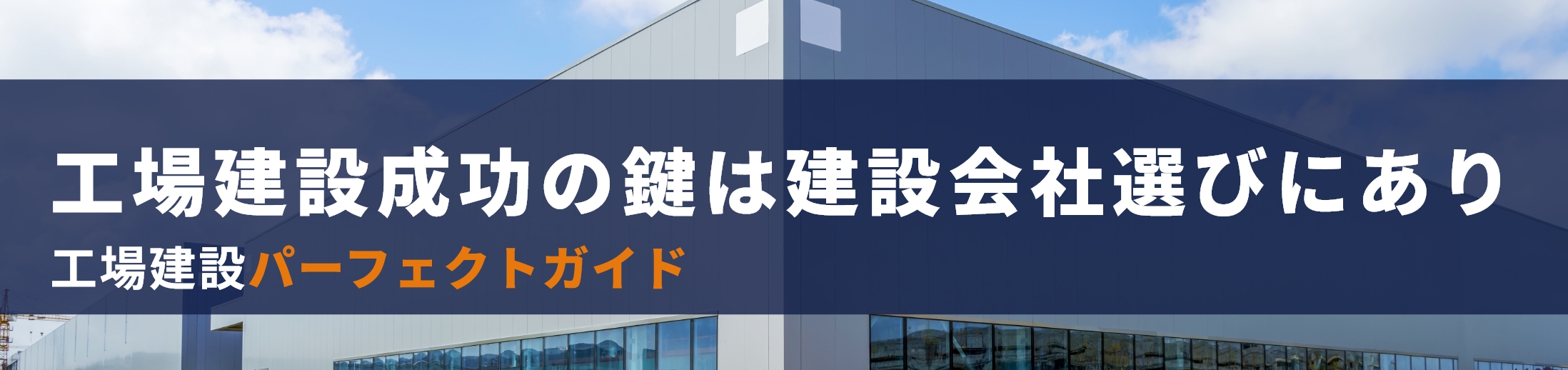