倉庫作業の効率化を実現!動線の分析が重要な理由 | 工場建設パーフェクトガイド
工場建設の情報
倉庫作業の効率化を実現!動線の分析が重要な理由
公開日:2024.10.31 更新日:2024.10.31
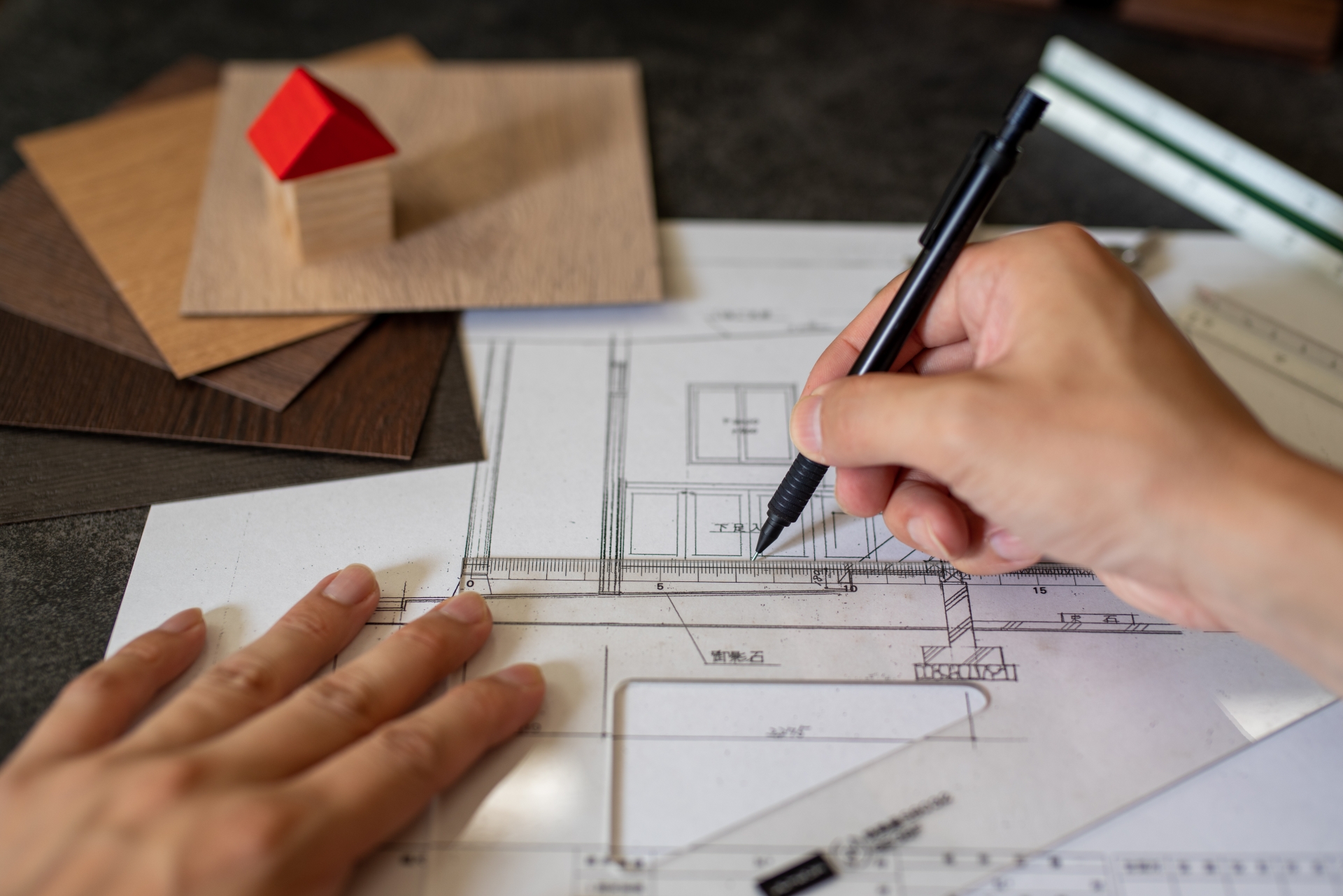
動線分析は、倉庫内の作業効率を向上させるために不可欠な手法で、物品や作業者の流れを視覚化し、効率的な動きを実現するものです。特に、新設の倉庫では、動線設計が不十分な場合に無駄な移動や接触事故のリスクが高まります。
動線分析により、物品の最適な保管位置や作業者の移動ルートを改善し、効率化と安全性を高められます。ABC分析やトラッキング技術の活用が効果的で、レイアウトを最適化することで作業効率や顧客満足度を向上させ、企業全体の運営コスト削減にも寄与します。
目次
動線分析とは?倉庫に必要とされる理由
倉庫の効率的な運営において、動線分析は欠かせない要素です。動線分析を行うことで、倉庫内の作業がどのように進行するかを理解し、効率的な動きを実現できます。特に、倉庫は多くの人や物が行き交う場所であるため、動線を最適化することが作業効率の向上やコスト削減につながります。
動線分析の定義とその重要性について、詳しく説明します。
◇動線分析とは
動線分析とは、作業や動作の流れを視覚化し、効率的に動くための分析手法です。工場や倉庫、店舗などさまざまな業種で用いられますが、倉庫においては特に重要です。倉庫内では、商品が入荷され、保管され、出荷される過程で多くの動きが発生しますが、これらの動きが無駄なく、スムーズに行われることが求められます。
動線分析では、各作業者の動きや物品の流れを詳細に調査し、どのように動けば効率的かを導き出します。これにより、作業の効率化だけでなく、安全性の向上も図れます。例えば、作業者が必要な物を取りに行く際に無駄な動きを排除し、効率的に作業を進められれば、全体の作業時間を短縮することが可能です。
◇倉庫レイアウトの最適化に不可欠
倉庫における動線分析は、レイアウトの最適化に不可欠です。倉庫の動線を明確にし、適切なレイアウトを設計することで、作業効率の向上や人件費の削減、さらには管理費の削減に繋がります。動線分析を通じて、各作業の流れを理解し、無駄を省けます。
例えば、商品を保管する位置や出荷する際の経路を見直すことで、作業者の移動距離を最小限に抑えることが可能です。これにより、作業者はより少ない時間で多くの作業を行え、効率的な業務運営を実現します。
さらに、動線分析は倉庫の安全性を向上させる要因ともなります。適切な動線を設計することで、作業者同士や機器との接触を減らし、安全な作業環境を確保できるのです。このように、動線分析は倉庫の運営において欠かせないプロセスであり、企業全体の効率を向上させるための重要な手段といえるでしょう。
新設の倉庫で起こりえるレイアウト課題
新設の倉庫では、適切なレイアウトがなければ効率的な運営が難しくなる場合があります。設計段階でのミスや考慮不足により、無駄な動線が生じたり、接触事故のリスクが高まったりすることがあります。
本章では、新設の倉庫で起こりうるレイアウトに関する課題を説明します。
◇無駄な動線が発生
新設の倉庫では、動線の設計が不十分であると、無駄な動線が発生することがあります。特に、物品の入出庫に際して必要な動きが多くなり、作業者が効率的に動けない状況が生じることがあります。例えば、入荷した商品を倉庫内で移動させる際に、不要な回り道を強いられる場合、作業の効率が大きく損なわれます。
また、作業者が必要な物を取りに行くために何度も移動することになると、その分の時間と労力が無駄に消費されてしまいます。これにより、物流作業の全体的な効率が低下し、企業の運営コストが増大する原因ともなります。
このような無駄な動線を避けるためには、設計段階で動線分析を行い、各作業の流れを明確に把握することが不可欠です。
◇接触事故
倉庫のレイアウトが適切でない場合、人や機器との接触事故が起こりやすくなります。倉庫内では多くの作業者やフォークリフト、商品が同時に行き交うため、接触事故のリスクが高まります。特に、狭い通路や不明瞭な動線が存在する場合、作業者同士やフォークリフトとの衝突が起こる可能性が増加します。
例えば、フォークリフトを使用して商品を移動させる際に、作業者がその通路に立っていると、思わぬ事故につながることがあります。事故が発生すると、商品が破損したり、作業者が負傷したりする危険が伴います。
そのため、倉庫内の危険箇所を特定し、レイアウトの変更を実施することが求められます。動線分析を行い、リスクの高い場所を把握することで、適切な対策を講じることが可能です。このように、倉庫のレイアウトにおいて接触事故のリスクを軽減するためには、慎重な設計と動線分析が不可欠です。
動線分析に役立つ手法
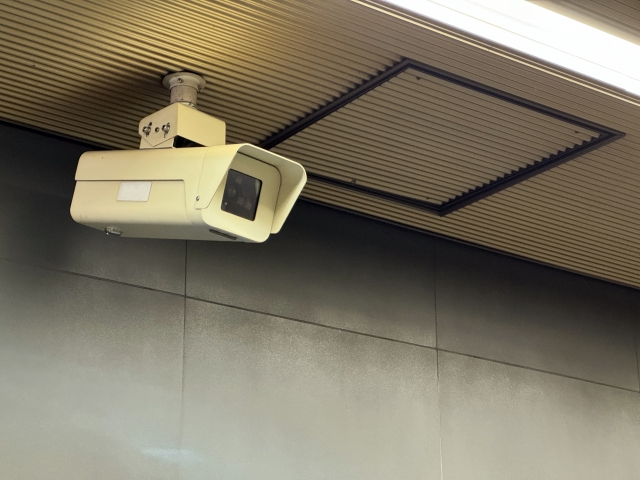
倉庫建設において動線分析を効果的に行うためには、さまざまな手法やツールを活用することが重要です。本章では、動線分析に役立つ手法として「ABC分析」と「ツールの活用」をご紹介します。
これらの手法を駆使することで、効率的な倉庫運営が実現します。
◇ABC分析
ABC分析は、倉庫内のアイテムを重要度に応じて分類し、効率的な管理を行う手法です。この分析方法では、アイテムの使用頻度や価値に基づいて、A、B、Cの三つのグループに分けます。
Aグループには高価値で使用頻度の高いアイテム、Bグループには中程度のアイテム、Cグループには低価値で使用頻度が低いアイテムが含まれます。これにより、重要なアイテムを優先的に管理し、ピッキング動線を短くすることが可能となります。
例えば、Aグループのアイテムを倉庫の出入口近くに配置することで、作業者が素早くアクセスでき、効率的な作業を実現できます。さらに、ABC分析によってアイテムの保管効率を上げることができ、倉庫の運営コストを削減することにもつながります。このように、ABC分析は動線分析を行う上で有効な手法であり、効率的な物流を支える重要な要素です。
◇ツールの活用
動線分析には、さまざまなツールを活用することで、より精度の高い分析が可能になります。例えば、カメラやセンサー、ビーコンなどを用いたトラッキング技術を導入することで、リアルタイムで作業者の動きを把握できます。
また、RFIDタグを活用することで、商品の位置情報を正確に取得し、動線分析に役立てられます。これらのツールを利用することで、無駄な動きや渋滞がひと目で分かり、改善点を迅速に把握することが可能です。特に、倉庫内での動きを可視化することで、作業者が効率的に動ける環境を整えられます。
このようなツールの活用は、動線分析を効果的に行うために欠かせない要素であり、倉庫の運営効率を大きく向上させることが期待されます。
新倉庫のレイアウトで最適な動線を確保
新たに倉庫を建設する際には、初期段階から適切な動線を確保することが重要です。設計時に動線を改善する事例や、配送の動線を最適化した事例を通じて、効率的な倉庫運営を実現する方法を探ります。
◇設計時点で動線を改善できた事例
倉庫の設計段階で動線を改善できた事例は多く存在します。例えば、設計者が動線計画を立てる際に、各作業の流れを詳細にシミュレーションし、無駄な動きが発生しないようにレイアウトを調整した事例があります。作業者の動きや物品の移動経路を検討し、必要なスペースを確保することが重視した結果、作業者の移動が最小限に抑えられ、作業効率を大幅に向上させることにも成功しました。
設計時点での動線の改善は、後の運営においても大きな影響を与えるため、十分な配慮が不可欠です。こうした設計段階からのアプローチは、長期的な運営の効率性を高める要因にもなります。
◇配送の動線を最適化した事例
ある企業では以前の物流体系において、商品の出荷までに多くの無駄な動きが発生していました。この課題を解決するために、物流の専門家が新しい提案を行い、動線の見直しを実施しました。具体的には、出荷する商品の保管位置を再配置し、必要なアイテムが近くに集められるようにレイアウトを変更しました。
これにより、作業者は必要な商品を迅速に集められるようになり、配送のスピードが大幅に向上しました。動線の最適化は、顧客サービスの向上にも寄与するため、企業にとって重要な施策となります。このように、倉庫のレイアウト改善は、効率的な物流だけでなく、顧客満足度の向上にも役立ちます。
動線分析は、倉庫内での作業効率を最大化し、安全な業務環境を構築するために重要な手法で、物品や作業者の流れを詳細に把握し最適化することを目的としています。
特に新設の倉庫では、動線設計が不十分な場合、作業者の無駄な移動や接触事故が発生するリスクが高まります。しかし、動線分析を行うことで、物品の最適な保管場所や作業者の効率的な移動ルートを見出し、倉庫内の作業効率や安全性を高められます。
動線分析においては、ABC分析やトラッキング技術の活用が効果的です。ABC分析では、倉庫内の物品を重要度や使用頻度に基づいてA、B、Cの3つのカテゴリに分類し、特に重要なアイテムを優先的に取り扱います。
これにより、頻繁に使用する重要な物品を作業者が簡単に取り出せるように配置することで、ピッキングの動線が短縮され、作業効率が向上します。さらに、作業者の移動距離を最小限に抑えることで作業時間を短縮し、結果的に人件費や管理費を削減することも可能です。
また、動線分析におけるトラッキング技術の活用も近年注目されています。例えば、カメラやセンサー、ビーコンなどを用いたトラッキングシステムを導入することで、リアルタイムで作業者の動きを把握できるようになります。
新設の倉庫では、初期設計の段階から動線の最適化が非常に重要です。新しい倉庫の設計段階で動線分析を行い、無駄な動線や衝突リスクを未然に防ぐことで、作業効率の向上が期待できます。
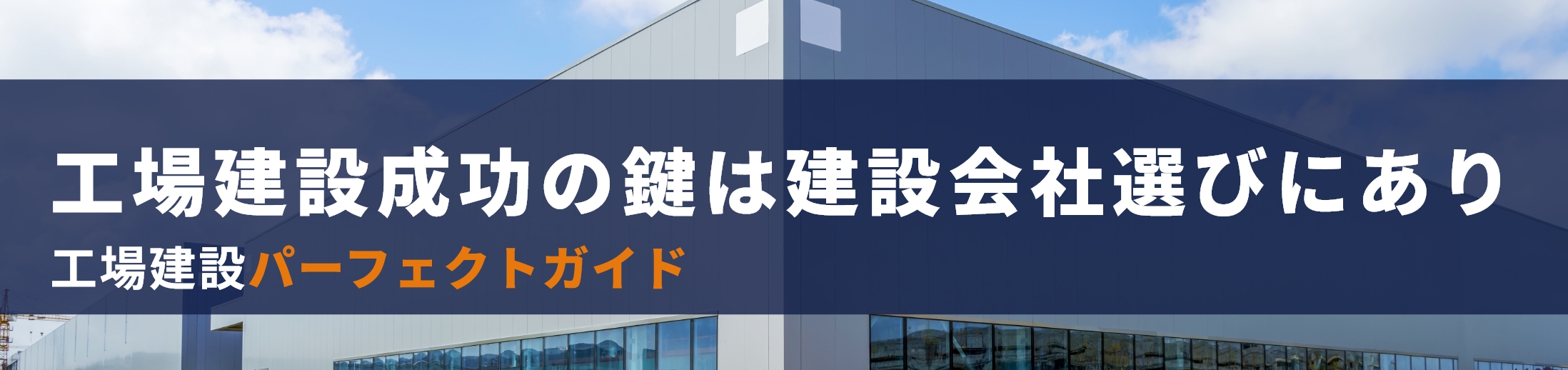